Turbina de Gas: Emplazamiento
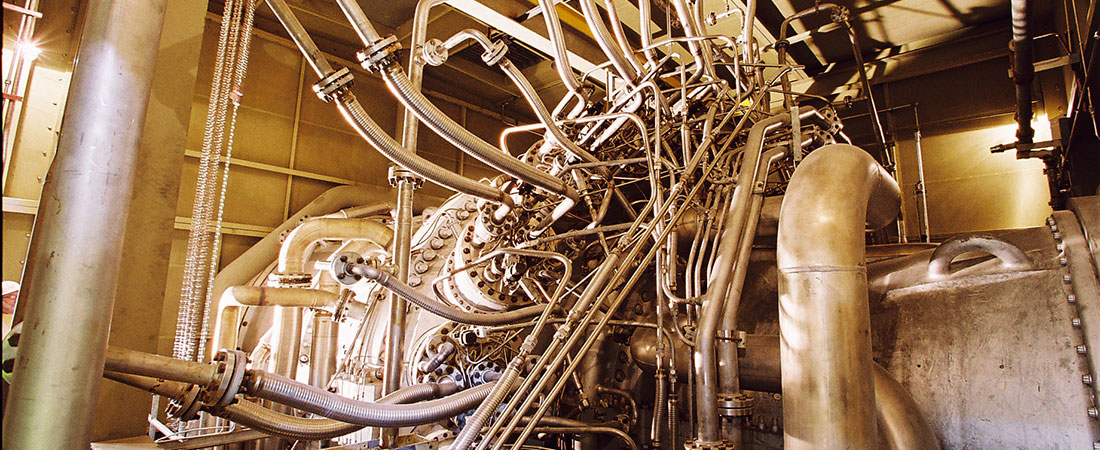
Datos principales:
- Potencia unitaria: 254 MW.
- Velocidad: 3.000 r.p.m.
- Ratio de compresión: 15,4:1
- Flujo de gases de salida: 640 kg/s.
- Temperatura de combustión: 1.300 °C.
- Temperatura de los gases: 609 °C.
Las turbinas son modelo MS 9001 FA, diseñadas y fabricadas por General Electric. El generador eléctrico está conectado con la turbina de gas mediante un acoplamiento rígido, y se sitúa en el extremo del compresor de turbina. El compresor de la Turbina de Gas dispone de 18 etapas con álabes guías variables para una optimización del rendimiento a cargas parciales. Los quemadores de turbina son del tipo de baja emisión de NOx. La turbina de gas tiene tres etapas. La carcasa del conjunto turbina-compresor es del tipo partido horizontalmente para unas rápidas y fáciles inspecciones y mantenimiento. El arranque del grupo turbogenerador es realizado mediante la motorización del generador (LCI). La turbina de gas emplea como combustible únicamente gas natural (aunque está capacitada para quemar gasoil) y sus gases de escape pasan a través de las calderas de recuperación para su aprovechamiento energético.
Caldera de Recuperación
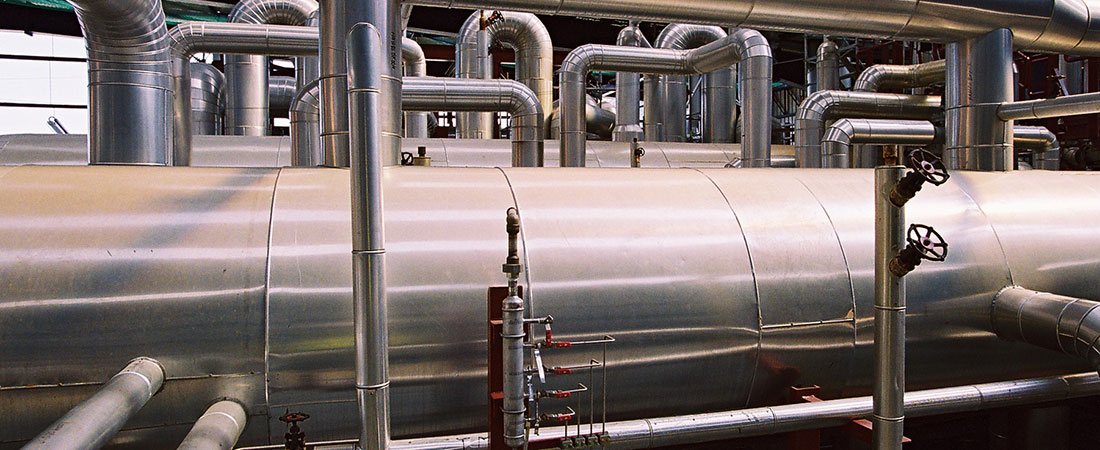
Datos principales:
- Presión del vapor AP: 127 barg.(*)
- Temperatura del vapor AP: 567 °C.
- Presión del recalentado caliente: 26 barg.(*)
- Temperatura del recalentado caliente: 568 °C
- Presión del vapor BP: 4 barg.(*)
- Temperatura del vapor BP: 274 °C.
(*) Presión relativa.
La central dispone de dos calderas de recuperación de circulación natural, diseñadas y fabricadas por BWE. Las calderas se ubican dentro de un mismo edificio y tienen tres niveles de presión y recalentador.
La caldera es diseño ASME y acorde a los requisitos de arranque y parada de las turbinas de gas, así como a los cambios de carga.
El conjunto de caldera incluye las siguientes secciones:
- Sobrecalentador de alta presión secundario.
- Recalentador secundario y primario
- Turbina de vapor: 281.823 kW
- Evaporador de alta presión
- Economizador de alta presión, alta temperatura
- Sobrecalentador de media presión
- Evaporador de media presión
- Economizador de alta presión, baja temperatura
- Economizador de media presión
- Sobrecalentador de baja presión
- Evaporador de baja presión
- Economizador de agua de alimentación
Los calderines y sistema de control de sus niveles están diseñados para asegurar un adecuado nivel de operación sin un excesivo caudal de purgas.
Turbina de vapor
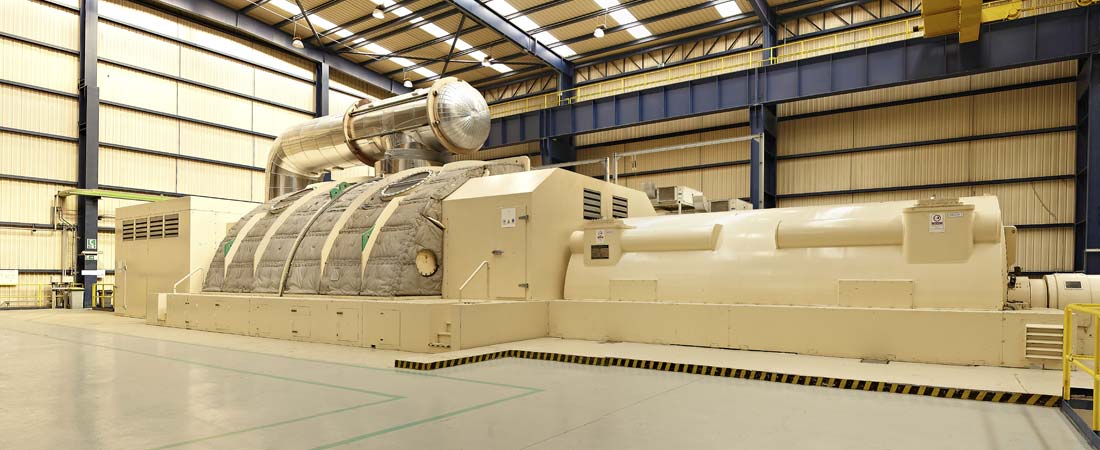
Datos principales:
- Potencia unitaria: 281 MW
- Velocidad: 3.000 r.p.m.
- Flujo de vapor AP: 540 t/h.
- Flujo de recalentamiento caliente: 640 t.
- Flujo de vapor BP (total): 670 t/h.
La turbina de vapor es de tipo condensación y recalentamiento intermedio, formada de tres cuerpos: alta presión, media presión y baja presión. Todos los módulos de turbina están seleccionados para las condiciones de vapor y caudal volumétrico específicos y disponen de las necesarias válvulas de parada y control en los cuerpos de alta, media y baja.
El vapor procedente de las dos calderas, se combina en una tubería común y es llevado al correspondiente cuerpo (AP, MP, BP) de la turbina.
El escape del cuerpo de baja presión es inferior y el vapor es dirigido al condensador situado bajo la turbina.
Con el fin de facilitar los arranques, paradas, así como permitir el funcionamiento de las turbinas de gas ante un disparo de la turbina de vapor, se dispone de los by-passes de alta, media y baja del 100% de la capacidad de producción de la caldera de recuperación.
Condensador
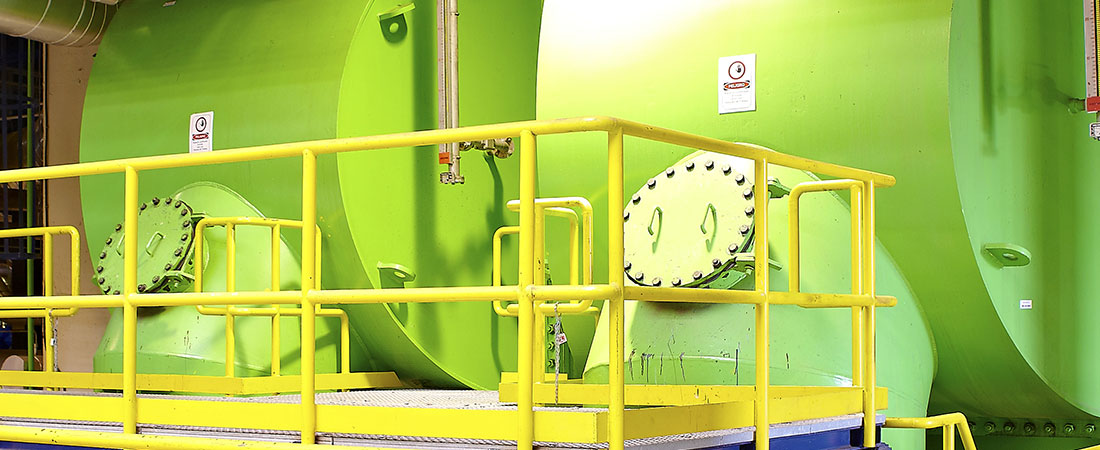
Datos principales:
- Flujo condensado: 200 l/s.
- Calor intercambiado: 471.000 kJ/s.
- Presión de diseño: 44,5 mbar.
- Temperatura de agua de refrigeración: 19 °C.
- Salto térmico en agua de refrigeración: 8 °C.
- Dimensiones: 19X8,6X8,4(h)m.
- Peso en vacío: 260 t.
El condensador de vapor es del tipo superficie de un paso, de tubos de titanio, refrigerado por agua de mar está diseñado, construido y probado de acuerdo con los Estándar de Heat Exchange Institute (HEI). La planta está diseñada para condensar el máximo flujo de vapor de escape de la turbina de vapor, para recibir los drenajes del sistema de vapor y para condensar los flujos de vapor de los sistemas de by-pass de AP, MP y BP, en condiciones de arranque del generador de vapor de recuperación de calor, arranque de turbina y disparo de la turbina de vapor.
Las cajas de agua y los tubos del condensador están diseñados y probados hidráulicamente para resistir las presiones resultantes de cualquier posible golpe de agua en el sistema de agua de circulación.
Ciclo agua-vapor
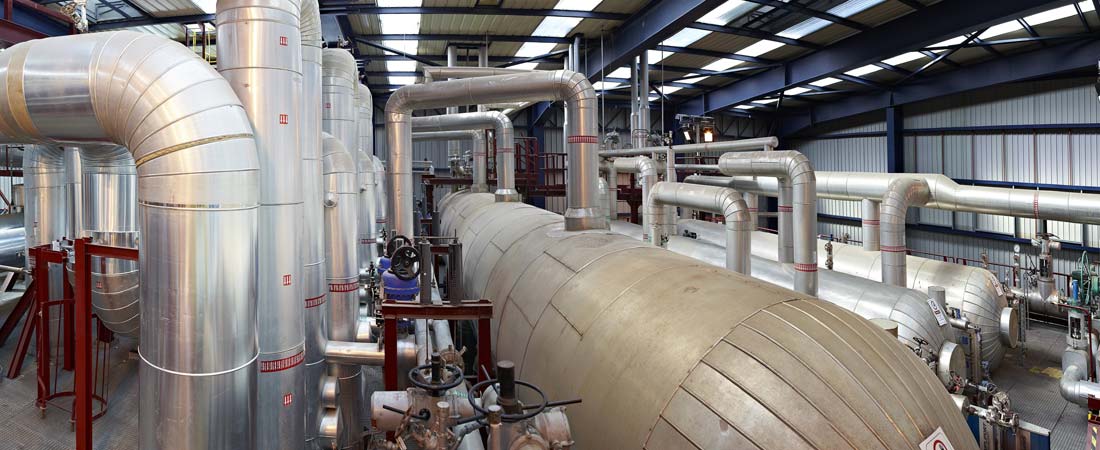
El vapor de alta presión producido en las calderas es llevado a través de una única tubería hacia el cuerpo de alta de la turbina de vapor. Allí es expandido y el vapor recalentado frío es retornado a través de una única tubería hacia las calderas, siendo repartido entre éstas. El vapor recalentado frío es mezclado con el vapor sobrecalentado de media presión y recalentado en los recalentadores de las calderas.
El vapor recalentado caliente se dirige hacia el cuerpo de media presión de la turbina de vapor.
El vapor de baja presión producido en caldera es parcialmente empleado como vapor de desgasificación. El exceso es sobrecalentado y dirigido hacia el cuerpo de baja presión de turbina a través de una única tubería.
El vapor expandido en la turbina es condensado en un condensador de superficie, de un paso, refrigerado por agua de mar. Al objeto de obtener altos rendimientos energéticos, la presión en el condensador ha sido optimizada.
El aire y los gases no condensables que entran o se producen en el circuito de agua-vapor, son extraídos en el condensador mediante el uso de bombas de vacío de anillo líquido.
El condensado acumulado en el pozo caliente del condensador es transferido al desgasificador mediante tres bombas del 50% de capacidad. Las líneas de succión de cada bomba son independientes, disponiendo de filtro para su protección.
El nivel en el pozo caliente del condensador se mantiene dentro de los límites establecidos, bien por la aportación de agua o bien por el desahogo de condensado hacia el tanque de reserva condensado.
El desgasificador ha sido diseñado para funcioamiento en vacío (aprox. 60°C) al objeto de obtener la mínima temperatura recomendada para alimentación de los economizadores de caldera, y así alcanzar el máximo aprovechamiento de los gases de escape de turbina de gas.
El tanque de almacenamiento del desgasificador es empleado como pulmón para compensar las diferencias de volúmenes dentro del circuito de agua vapor durante los arranques, paradas, operación en contínuo o cambios rápidos de carga.
Los gases extraídos en el desgasificador se dirigen hacia el condensador, a través de la conexión existente entre la cabeza del desgasificador y el cuello del condensador.
El agua de alimentación es transferida a caldera mediante dos grupos de bombas; de alta presión y de media-baja presión.
El grupo de alta dispone de tres bombas del 50% de capacidad para alimentar las dos calderas, y el grupo de media-baja dispone de tres bombas del 50% de capacidad.
En caso de fallo de alguna de las bombas de un grupo de alimentación, la tercera bomba arranca automáticamente.
El sistema dispone de dos by-passes de alta presión (uno por caldera), dos by-passes de media presión (uno por caldera) y un by-pass común de baja presión. Este sistema de by-passes, es empleado en las siguientes situaciones:
- Proceso de arranque controlado
- Proceso de parada controlada
- Rápidos cambios de carga
- Transitorio ante disparo de turbina de vapor
- Transitorio ante rechazo de carga
- El sistema de by-pass diseñado para trabajar con el 100% de la producción de las calderas de recuperación.